
The broadcasts of the recent royal wedding sounded pretty good to me despite the fact that the majority of the absorbtion in the room was people. However, split concrete blocks with a coarse surface can sound pretty good as diffusers.ĭiffusion while expensive is not to be underestimated. Paint it and close the pores and its almost as nasty-sounding as glass or tile. Sound absorbants are interesting when you consider that unpainted cinder block is about 1/3 as absorbant as high density fiberglass of similar area and thickness. I guess that people who work in factories with lots of cotton fiber dust in the air for decades can get a kind of lung disease, but casual work with sound absorbers doesn't usually involve that sort of thing. Polyester and cotton batts can be messy, but they aren't nearly as nasty to work with a fiberglass or rock wool. I think that rock wool is a bit nastier than fiberglass, but the difference is the difference between very ugly and very, very ugly. In either case wise people wear particulate masks, cover their bodies with long pants and long sleeves, and change their clothes and bathe within minutes of walking off the job. My house is insulated with rock wool, and the attic of our sanctuary at church is insulated with loose fiberglass.

What is different is how it feels to work with the various materials. Given a certain kind of fine fiber and a certain packing density, they absorb sound by means of the same basic physical process and the results are pretty much the same. My friends who pursue this kind of thing in the lab tell me that there is no magic related to fiberglass versus rock wool versus polyester versus cotton versus whatever. So, if I had made my sound absorbers out of 2" thick fiberglass batts of the kind used as thermal wall insulation, the absorbtivity at say 100 Hz would have been far less and the quality of the results would have been audibly diminished. A friend of mine who does lab tests on these things says that it is very hard to pack these kinds of fibrous materials so tighly that they turn into reflectors. Higher density products seem to absorb lower frequencies better, which is why the materials used for acoustical treatments are generally far denser than the ones made for thermally insulating walls and ceilings. Absorbers can also be made out of cotton or polyester, but those alternatives seem to be more costly. If it is 2" thick, composed of fine fibers, and its density is about 5 pounds per cubic foot (which makes it like a board) then it probably does about the same thing to sound waves. Johns Manville and others have competitive products, and other products made from mineral wool have similar acoustical properties.
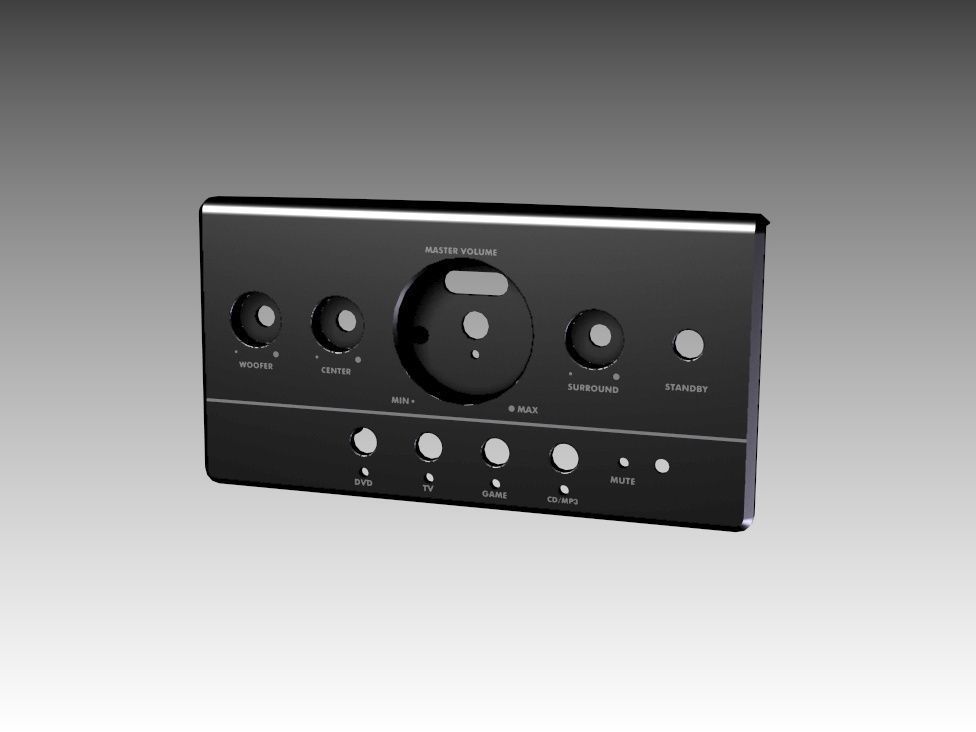
Exactly, and the unfaced products are what you want for just about any acoustics application.
